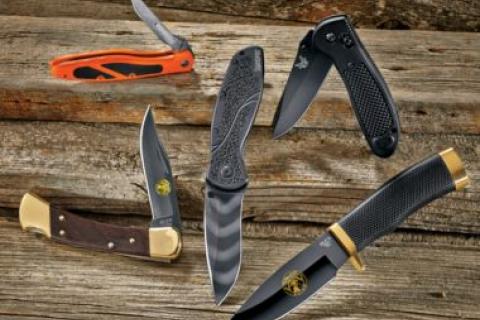
Whether you’re hunting, camping, butchering or just going about your everyday business, the right knife makes life much easier. But which knife is the right one? Simply typing in the word “knife” into an Internet search and hitting enter pulls up an overwhelming amount of options. Heck, even narrowing it down and typing something as specific as “skinning knife” leaves you with seemingly countless choices. But don’t worry – this buyer’s guide will help you whittle down the choices so you can pick the exact knife you need.
Knives by Application
•Boning – Should have a thin blade 5" to 6½" in length. You’ll want a fairly stiff blade for boning out big game, while a flexible blade is preferred for turkeys or upland birds.
•Skinning – Generally short with a deep drop, limiting the area of impact. Ideal for working in tight areas when caping an animal.
•Slicing – Have a narrow, thin blade, usually 8" to 12" in overall length and are effective when cutting ultrathin slices of meat. The more flexible the blade, the easier cutting thin slices is. Specialty slicers have a curved or scimitar-style tip to assist in tight spots, like between the wing and breast of birds.
•Everyday-Carry (EDC) – Should be small and light. However, if your knife is excessively small, some of the tasks you run into throughout the day may be too much for it to handle. A knife with a 3" blade is often a good balance between compactness and functionality, but this may not be perfect for everyone. Consider what you do most on a daily basis when deciding which EDC to purchase.
•Tactical – Designed for self-defense, but many can double as EDC knives. They are typically dark in color to aid in concealment. Easy-to-conceal folding-blade tactical knives generally have assisted opening for fast access. Deep-pocket clips that mount close to the end of the handle are often used so little knife is visible when it’s clipped to a pocket. Fixed-blade knives are harder to conceal and carry, but they’re stronger and provide instant access.
•Replaceable-blade – With these knives, you’ll never have to sharpen a blade again. The blades are dispensable and replacements are relatively inexpensive, so when one blade becomes dull, you simply change it out for one that’s razor sharp. These are used for many applications, from skinning to slicing.
•Fixed vs. folding blade – Fixed-blade knives are stronger, while folding blades are more compact and thus easier to carry.
Blade Materials
Blades are made of a wide variety of materials, and each has its own advantages. There is upside and downside to every material. Here is a breakdown of the most common materials you’ll encounter when shopping for the ideal blade.
•Crucible – Developed by Crucible Steel for the cutlery industry and known as the pinnacle of knife-making metals. It’s tempered for hardness, making it excellent at holding an edge. Also, it’s extremely corrosion-resistant, ensuring it will last for years, but fairly hard to sharpen.
•High-carbon steel – Also called cutlery steel. Holds an excellent edge and is easy to sharpen. A higher carbon content means increased blade hardness. The downsides to high-carbon steel are that it’s somewhat brittle, has a tendency to rust and reacts to both acids and alkalis, causing it to discolor. The discoloration doesn’t affect its performance.
•Stainless steel – Excellent if you want a blade that doesn’t discolor, but this alloy is a real chore to sharpen once it loses its edge. However, the extreme hardness does help the blade hold its original edge longer.
•Titanium – Good for all-purpose knives. Lightweight, durable and retains sharpness longer than steel. Relatively easy to sharpen. Titanium-coated knives or knives with titanium edges don’t have the same quality as those made purely of titanium or titanium alloys. Since sharpening removes metal, titanium-coated blades have a shorter life span.
•Ceramic – Lightweight, hard, dense space-age material that is stronger than steel, but far more brittle. Ceramic blades hold an edge significantly longer than steel and can be manufactured into much thinner blades, which makes cutting considerably easier. They are best used for slicing and should never be used for chopping due to their brittleness. Unlike steel, their hardness makes them impervious to chemical reactions with either acidic or alkaline foods. Diamond hones are used for sharpening and repairing chips.
Construction
A blade’s hardness is determined by using a Rockwell machine that forces a small penetrator into the metal’s surface. The depth of penetration is correlated to an A, B or C scale reading called the Rockwell hardness scale. A higher number is assigned to harder steel that allows less penetration. Blade steels are measured on the "C" scale (Rc) and range from Rc 55-60. In comparison, a diamond will range in the 80s on the Rockwell "C".
Stainless steel bears a number of industry designations, generally with a number such as 154 or 420, followed by alpha characters like CM or HC. The numerical value indicates the amount of each element used, and the letters reveal the alloys that were used. 154CM is a high-carbon, high-alloy stainless steel made with 1.05% carbon, 0.5% manganese, 0.4% - 0.55% Molybdenum and 14.0% chromium. Therefore, the 154 indicates 1% carbon, 0.5% manganese and 0.4% molybdenum. The CM indicates chromium. This grade of steel is widely used by top specialty-knife makers. The chart below compares the most common blade materials in terms of hardness, corrosion resistance and edge quality.

•Forged – Typically high quality and recommended for most applications. A prominent bolster between handle and blade will usually identify a forged knife, although a few are made without a bolster. They are usually heavier, better balanced and easier to keep sharp. Also, with care, they can last for generations.
•Stamped – Cut or stamped out of flat metal stock. They don’t undergo the numerous steps associated with forging and are thus lighter in weight and usually not as well balanced. Since the metal is not as dense as a forged knife, stamped knives won’t hold their edge as well.
•Sintering – An innovative process that results in all the durability, flexibility and light weight of titanium, plus the incredible edge retention of ceramic materials. Unlike ceramic blades, sintered titanium knives can be resharpened with standard sharpening stones. Some forged knives have parts that are manufactured separately and sintered together to form a knife of good quality at a lower cost than forged knives.
Blade Types
•Spear point – Symmetrical geometry on its point and down the blade give it two identical edges.
•Trailing point – Cut upward, higher than the spine of the blade. Excellent for skinning and caping.
•Sheepsfoot – Has a blunt, rounded tip and straight cutting edge. The lack of a traditional point reduces the chances of accidental punctures. Great for cutting around inflatable watercraft, livestock and during emergencies.
•Drop point – Largely popular. Common and especially useful in EDC knives. It has a lowered point that provides control and adds tip strength.
•Clip point – Similar to the drop point. An excellent all-around knife. It has a lowered tip with a long belly area that punctures well and is great for slicing.
•Tanto point –Specializes in piercing. It has a thick point that absorbs impact well.
•Gut hook – Used for skinning and field dressing. The hook is used to split the skin, unzipping the animal.
•Saw blade – Has a toothed edge that cuts when force is applied and a back-and-forth cutting motion is employed. Used to cut through hard material such as bone or wood.
•Saw blade – Curved tip reduces possibility of punctures when working in tight areas. Good all-purpose blade.
Edges
•Plain – A sharpened edge with no serrations or teeth – sometimes referred to as a smooth edge. Excellent for slicing, control, and accuracy. Produces clean cuts.
•Serrated – A more aggressive, saw-like cutting edge. Although they produce unrefined cuts, serrated blades retain their ability to cut long after straight blades have lost their edge.
Blade Grinds
•Hollow – Produces an extremely thin edge that is excellent for slicing. Many hunting knives use this grind.
•Chisel – Only ground on one side. This creates an extremely sharp knife. However, it isn’t symmetrical, forcing the knife to curve when slicing, thus making accuracy difficult.
•Sabre – Leaves a fairly thick edge that is ultrastrong, making it excellent for chopping.
•Flat –Excellent at slicing yet strong enough to chop. Ideal for kitchen cutlery.
•Convex – Essentially the opposite of a hollow grind. This leaves a lot of steel behind the edge, making it extremely strong – excellent for jobs that require a lot of force.
Blade Finishes
There seems to be countless blade finishes on the market, all with unique names. The purposes for blade finishes range from purely cosmetic to rust resistance to friction reduction. Below are the most popular coatings. Many finishes fit into one of these categories even though they may have a different, brand-specific name.
•Black electroplating – A nonreflective coating bonded to steel using an electrostatic process. It reduces the steel’s reflectivity.
•Teflon® – Slick and cuts better because of reduced friction.
•Satin – Has a medium luster. Shows fine buffing lines with two directional finishes that better display the bevels of a blade. Used for cosmetic purposes.
•Black-coated – Gives the blade a dark matte finish. This helps with concealment. Also ups a knife’s corrosion resistance.
Lock and Joint Mechanisms
•Lockback – Similar to a fixed-blade knife, though still not as rigid. When opened, this blade locks into position, giving it more strength and stability.
•Slip joint – Blade doesn’t lock. Rather, it’s held in place by a spring device that allows the blade to fold when a certain amount of pressure is applied.
•Frame and liner locks – Can be opened easily with one hand. Most often used on folding tactical knives.
Handle Materials
•Wood – Offers an excellent grip but requires regular care. Keep it out of water and rub occasionally with mineral oil.
•Plastic – May become somewhat brittle in time and can be slippery in the hand. Plastic-impregnated wood has properties similar to wood but requires less care and lasts longer.
•Synthetics (G10, Kraton, Micrarta, polymide, etc.) – Provide phenomenal grip and comfort, plus they last longer than natural materials.
•Metal – Fairly indestructible when used for handle material. Can be slippery or firm – many knives have a patterned metal grip, which provides a solid grasp in all conditions.
Blade Finishes
There seems to be countless blade finishes on the market, all with unique names. The purposes for blade finishes range from purely cosmetic to rust resistance to friction reduction. Below are the most popular coatings. Many finishes fit into one of these categories even though they may have a different, brand-specific name.
•Black electroplating – A nonreflective coating bonded to steel using an electrostatic process. It reduces the steel’s reflectivity.
•Teflon® – Slick and cuts better because of reduced friction.
•Satin – Has a medium luster. Shows fine buffing lines with two directional finishes that better display the bevels of a blade. Used for cosmetic purposes.
•Black-coated – Gives the blade a dark matte finish. This helps with concealment. Also ups a knife’s corrosion resistance.
Lock and Joint Mechanisms
•Lockback – Similar to a fixed-blade knife, though still not as rigid. When opened, this blade locks into position, giving it more strength and stability.
•Slip joint – Blade doesn’t lock. Rather, it’s held in place by a spring device that allows the blade to fold when a certain amount of pressure is applied.
•Frame and liner locks – Can be opened easily with one hand. Most often used on folding tactical knives.
Handle Materials
•Wood – Offers an excellent grip but requires regular care. Keep it out of water and rub occasionally with mineral oil.
•Plastic – May become somewhat brittle in time and can be slippery in the hand. Plastic-impregnated wood has properties similar to wood but requires less care and lasts longer.
•Synthetics (G10, Kraton, Micrarta, polymide, etc.) – Provide phenomenal grip and comfort, plus they last longer than natural materials.
•Metal – Fairly indestructible when used for handle material. Can be slippery or firm – many knives have a patterned metal grip, which provides a solid grasp in all conditions.
- 3818 views